Sometimes the Grass IS Greener on the Other Side
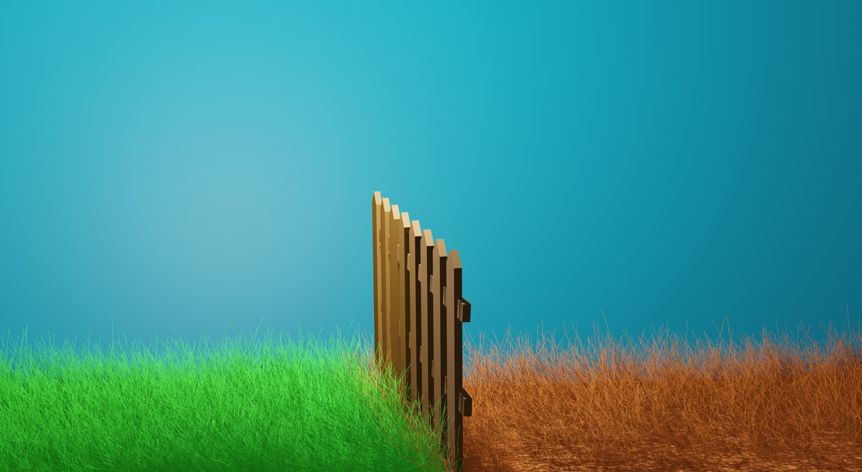
Today, many are discovering the process of offsite modular construction. While they study and research it, they haven’t made the leap to it… yet. It’s hard for many homebuyers and homebuilders to believe that a different way is a better way. They are still stuck on traditional construction methods as a tried-and-true way.
Much like the early 1900s when Henry Ford is attributed with the quote, “If I had asked people what they wanted, they would have said faster horses”. While he probably never actually said it, the point is still made. Humans find it hard to change or think differently. But sometimes you just have to. Up to this point, everything we buy is built in a factory – except our home. The single biggest asset most people will ever buy is still built much like it was in 1830. A better way to build is there. We are just one step away from a better way to build. Modular construction is what’s on the other side of the fence!
Modular Construction Means a Home is Built Better
Today’s site builders always refer to stick-built homes as if they should equate to a quality-built home. Actually, the opposite is true. Think about it. Do you believe workers can work in the mud, wind, heat, cold, etc., on unlevel ground and measure and cut lumber accurately? Do you believe walls and floors can be built with precision and consistency outside? Can windows and house wrap be installed properly from ladders? Most stick builders have dabbled in off-site construction. That is what a roof truss or a floor truss is. And why are stick builders using them? Because they know they are stronger, built consistently better, and are cheaper than doing the same thing onsite. However, they just won’t apply off-site construction to the rest of the houses they build.
A system-built home takes it to the next level. Instead of just using roof trusses or floor trusses, the whole house is built using systems. With modular construction, this could be subcomponents that are built and then installed into larger components. Those components get installed on the floor assembly. Walls are built and installed on the floor assembly. Ceiling/roof assemblies are built and installed on the larger assembly completing a volumetric “box”. The complete construction process is engineered. The weather has no impact on the precision of a cut. Water doesn’t get on floors to be absorbed into the wood. A home is built efficiently and cost-effectively. Waste is minimized. Reduce, reuse, recycle is the theme in systems-built construction.
Homes are Safer
Modular construction, by definition, is built-in modules. These modules each have to be built strong individually. In addition to meeting the minimum building code, they have to be built stronger and actually exceed building code to simply make the trip to your home site. Have you ever watched a module of a modular home being transported on the highway? It has to be able to travel on the road at 65 miles per hour, be maneuvered into position at a home site, and then lifted by a crane with as little as two cables to be safely placed on a foundation. Every modular home has essentially been through a hurricane and an earthquake before it is ever actually lived in.
Within each module, a continuous load path is created by virtue of its factory construction. A floor is built in a systematic manner. The wall partitions are built and installed on that floor. They are attached securely to the floor and to each other. The ceiling/roof assembly is then built as a component and installed on the top of the module. This roof/ceiling assembly is then attached to the wall structure. In addition to the straps, lag bolts, and screws used in the module, in many factories, a sheathing product known as TallWall is also used. This product is essentially longer OSB sheathing. In addition to its benefit of reducing air leakage for a more energy-efficient home, it offers strength to the home by adding an additional layer of connectivity between the floor, wall, and roof system.
Once on-site, even the process of assembling the modules increases the inherent strength of the completed home. For example, with a two-story home, two modules are placed on the foundation. These modules are then connected to each other under the floor and above the ceiling using bolts or lag screws. The modules for the second story are added and again, the area of the modules that adjoin each other are connected using bolts are lag screws. The perimeter of the exterior of the modules is connected using either straps, nails, or OSB, maintaining and even enhancing the continuous load path of the home. The first floor is then connected to the foundation, and the continuous load path is completed. The fully assembled modular home is much stronger than its site-built counterpart.
Homes are More Energy Efficient
Using modular construction to build a new home is even better for making homes more energy-efficient. Homes built outdoors tend to absorb moisture. As a home dries out and releases the moisture that was trapped during the construction process, gaps and other cracks tend to appear. The multitude of tiny openings in your home’s building envelop collectively creates a huge opportunity for air to escape, drastically reducing the energy efficiency of homes built onsite and exposed to the elements. This is just another reason why we choose to use superior modular construction when building custom homes for our clients.
With the growing interest and demand for energy efficiency, Impresa Modular takes pride in providing the most energy-efficient home possible. As an Energy Star partner, Impresa Modular offers several items as standard that meets or exceeds current Energy Star, LEED, and Green Building Standards. Our homes provide you with the option to customize any of our home plans to meet or exceed the requirements for the certification of your choice. If it’s an optional Energy Star Certified home you require, Impresa Modular will enlist a third-party Energy Star rater to guarantee your custom home meets or exceeds the prevailing requirements specified by Energy Star. It’s just one more way to meet the needs of customers that require a higher standard for their energy-efficient home.
Modular Homes Deliver on Value
Most that have researched using modular construction for building their new custom home find many reasons that make it an attractive option. Indoor construction means water doesn’t get into the home and creates mold and mildew issues, while quality is enhanced because of the assembly line controls and oversight. But most never discover that one of the key reasons that modular homes can be provided at a great value is because of their leading-edge material and waste management techniques.
RELATED: WHAT IS YOUR HOME PURCHASING POWER?
By concentrating the construction of so many homes in one location, modular home factories are able to sustainably manage their construction waste. Everyone wins! Homebuyers get their home for a better value, landfills don’t accumulate unnecessary waste, and the factory lowers its cost of construction. Modular construction provides the environmentally responsible way to build a custom home at a great value!
Modular Means More
Most custom builders have struggled for years to embrace the rise of modular construction. However, the internet has become a tremendous resource for home buyers building a new home. Today’s home buyers are doing the research. They are learning about the advantages that modular construction provides. They are learning about the difficulties that the construction industry is having with labor and the resulting issues it is causing in new home building. Today’s home buyers want more. The more homebuyers learn about modular construction and its benefits, the more they are demanding it. They are ready for the new normal of building homes using modular construction. Homebuyers are ready to trade in the horse for a much better method of transportation!
The post Sometimes the Grass IS Greener on the Other Side appeared first on Impresa Modular.