Modular Construction: The Solution for Failure in the Field
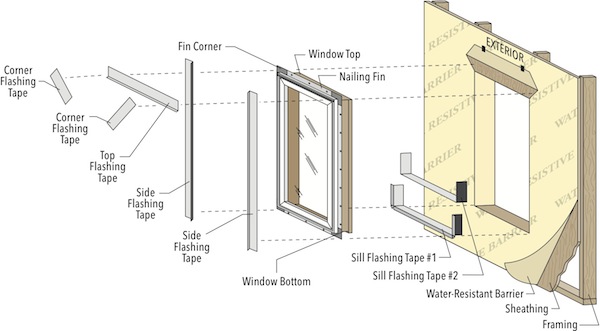
If I get up to go to work in the morning and my car doesn’t start, all I know is that my car didn’t start. When my printer jams, if my cell phone won’t turn on, or the washer leaks, all I know is that I have just experienced an unwanted outcome. At that moment, I don’t really care why my coffee maker isn’t making my morning coffee. My first thought is “now where do I get a cup of coffee?” What do you think about if you experience a leaky window in your home? Is it the window itself that is leaking or is water coming in around the window? With today’s home construction, most of the time it is because the window was installed improperly.
Is it a Product Problem or an Installation Problem
Think of all the issues you have in your current home. Do you have a leaky window?… laminate flooring that is peeling?… drafty areas or cold rooms in your home? Most often initial blame goes to the product. Most products are tested to rigorous industry standards to earn various seals, such as UL listings, etc. Not to say that some products don’t fail. Factories are building large volumes of windows, millions of feet of flooring, and thousands of heating systems. When building that many items you are bound to have some small failure rate.
However, most of the time, the failure of the product or the missed expectation of its use can be traced directly back to its improper installation. Let’s use the leaky window, for example. Most windows are manufactured to a precise specification. They are tested and perform according to that specification. Occasionally a seal can break or a corner can crack. A cracked corner can lead to water leakage in a home. However, most often that water leakage can be traced back to the improper installation.
RELATED: BUILDING HOME VALUE BY REDUCING CONSTRUCTION WASTE
Imagine your new two story home has to have a window installed on the second floor. The window opening is cut and ready for the window. The window is delivered to the site. The installer has to pick up this window that weighs over 50 pounds, climb a ladder (that is set on uneven ground) that may or may not be long enough to reach where he needs to be, and he needs to hold it level and install it correctly. Now imagine its 97 degrees and humid. His partner didn’t show up to work and he has to install the window by himself. What are the odds that the window manufacturer’s installation instructions were followed exactly? … Exactly! The odds are that membranes weren’t applied correctly. The house wrap wasn’t cut, layered, and taped. And perhaps, since they were going to be covered, all of the required nails weren’t used to secure the window to the sheathing.
Your Home Isn’t Built in a Lab
Almost half of the counties/jurisdictions in the U.S. don’t require home inspections while a home is under construction. Let’s use insulation as an example. Insulation is typically rated by its R-Value. The higher the R-Value the more resistance the insulation has to heat loss. The R-Value can actually change by temperature and all of that is controlled, measured, and reported on by lab testing. In the lab it is dry, precisely installed for testing, and evaluated.
Now, let’s take that same insulation and see how it performs in the field (in your new home). Your home has things called studs which are typically made of wood and that are structural and needed to support your home. Insulation is placed between them. Let’s say the insulation has an R-Value of 19 on the wrapper. How does insulation installation fail in the field?
Crushing/Compression – Insulation has to be installed at its full thickness to function to the manufacturer’s specification. If you place insulation in a 4” wall that should be in a 6” wall, you just reduced its effective R-Value.
Not applied Stud to Stud(gaps) – Insulation installation is graded by how well or how poorly it is installed. In the field, if there is an inspection, the inspector just checks to make sure that the correct R-value insulation was used, not if it was installed properly. The best rating is a grade I install, the worst is grade III. Air and cold can leak in through the gaps between the studs and the insulation. A grade III will equate to higher energy bills!
Drooping/Cut short – Many home’s today have 9’ and even 10’ ceilings. The average height of a construction worker is approximately 5’ 10”. Do you think they can reach to the top of the wall to insure that the batts of insulation were placed properly against the top plate of the homes wall cavity? If they run out of insulation, do they fill the small area at the bottom of the wall?
Cut around outlets/irregular areas – Your home is full out outlets and switches. How do you get insulation there? Do you notch the batt of insulation? Do you push it behind the outlet box? Do you kind of bend the insulation around the box? Have you ever put your hand beside an outlet on a cold windy day? Did you feel air movement or the cold?
Every one of these issues compromises the installation of the insulation thereby reducing the effective R-Value of insulation. The R-Value in the lab is far different from the R-Value you are actually getting when your home is built outside.
There’s an App for That
As a contractor licensed/registered/certified in most of the U.S., continuing education is required. There is one person that stands out for delivering that education to many builders in states that require continuing education. Mark LaLiberte is a national speaker and an instructor on the benefits of constructing durable, energy efficient and healthier homes. He is a true expert in the field. He is a partner in a company called Construction Instruction.
Coincidentally, they have a free app called Construction Instruction. This mobile construction app has home construction videos, animated building details, building science articles, and building product & materials installation info, technical data, and other ‘Best-Practices’ information. It is completely animated so language isn’t a barrier to its use. Everyone has a phone or tablet. It is a tremendous resource to see exactly how to install practically any product when you need instruction that is easy to follow.
Modular Homes: Not Built in a Lab, But Built Indoors
When it comes to choosing where your home is built, you have options. While the laboratory is great for testing, it isn’t where homes are built. However, where homes have been traditionally built (outside and exposed to weather) isn’t the best place. Modular homes are constructed indoors and under roof. Your home never sees the rain on its floors or in its walls. The workers who build your home work every day of the week. They aren’t building in the sun or on a 100 degree day or a 10 degree day.
The materials aren’t subjected to UV light before they are covered. Moisture isn’t trapped in the home. The factory is specifically designed to ergonomically allow workers to construct, install, and complete components of your home so they meet manufacturer’s specifications each and every time. The next time you see a home with a leaky window or feel a draft, think about how building your next home indoors could change your experience in your next home.
The post Modular Construction: The Solution for Failure in the Field appeared first on Impresa Modular.