Building Systems Win Big in Construction Scrabble
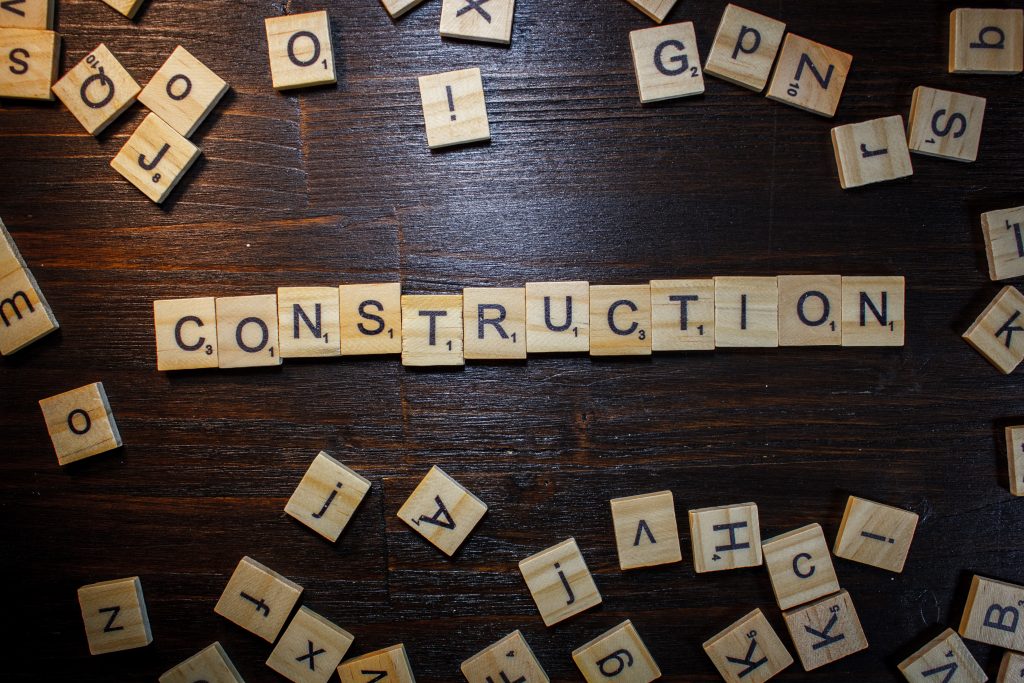
In the world of Construction Scrabble, Building Systems Win Big! In Scrabble, Building Systems score a 24 while Site Built scores an 11. While this is just a metaphor, it illustrates a point.
S1 | I1 | T1 | E1 | B3 | U1 | I1 | L1 | T1 | 11 | |||||||
B3 | U1 | I1 | L1 | D2 | I1 | N1 | G2 | S1 | Y4 | S1 | T1 | E1 | M3 | S1 | 24 |
In today’s world of flat and falling productivity in home construction, building systems can give a builder the edge they need to provide a better quality home. Using Building Systems can also give a homeowner the peace of mind knowing that their home was built with the quality and precision that can only be achieved using indoor construction.
What is a Building System?
Most people are familiar with traditional home building, commonly called site built construction. When you drive by a community on your way to work or see a custom home being built on an individual property, it is typically being constructed onsite. The process you see hasn’t changed much since the 1830’s. The biggest improvement was platform framing that was first introduced in the early 1900’s.
A building system is essentially a highly engineered process of producing buildings or components of buildings in a highly cost-effective and efficient manner. Most people are familiar with something called a roof truss. It’s a prefabricated wooden structure that integrates a triangular webbing of structural members to provide support for the roof above while tying the outside walls of the house together. Since its invention in 1952, it has become the most popular way to build a roof quickly. Why? Because it is highly engineered, cost-effective, and vastly speeds up the roof construction process.
Yes, the construction industry is slow, but it gets there… so, in 1970 floor trusses were invented. They too have come into common use for exactly the same reasons. They are also a product that is highly engineered, cost-effective, and they vastly speed up the floor construction process.
Almost every residential builder today would not imagine building a home without using roof trusses and even floor trusses. Why? Because they are strong, pre-built (built offsite then delivered and set), and cheaper than building those same components on site (Are you starting to get the point?).
Can You Build a Complete Home with a Building System?
The answer is yes. Components of a home can be built using building systems, and those components can be combined into the larger component of a home. The National Association of Home Builders recognizes four types of construction using building systems: Modular Home Building, Panelized Home Building, Concrete Home Building, and Log and Timber Home Building. Here is an overview of each system:
Panelized Home Building – Within panelized home building, there are several subcategories. Two of the main ones being basic panelized construction and another one known as Structural Insulated Panels (SIPS). Using basic panels, a home plan is divided into wall and roof sections and are framed off site in a factory. The panels are then loaded flat on large trucks and delivered to the site. Each panel is coded and the entire home is assembled, much like a puzzle with the coded pieces. However, the panels typically do not contain plumbing, electrical wiring, and finished interiors or exteriors. This requires all of the onsite completion by trades, the same as is typical with traditional onsite construction.
SIPS is considered a high-performance building system that consists of an insulating foam core that is sandwiched between two structural facings. These facings can be OSB, fiber-cement board, etc. SIPS are considered one of the most airtight and well-insulated building systems making them an inherently green product. With SIPS, the plumbing, wiring, and interior/exterior finishes have to be completed onsite as is typical with traditional construction.
RELATED: Constructuring: The Future of Home Building?
Concrete Home Building – Most think of concrete construction for commercial buildings. However, there has been a growing interest and use of concrete for residential construction. There are several methods to utilize concrete including Insulating Concrete Forms (ICF), Panel Systems, and Removable Forms (cast in place). ICFs have established themselves as environmentally friendly and consist of modular blocks or panels that encase concrete between two layers of insulation.
Panel systems are typically precast and then placed with a crane. There are precast panels that are cast offsite at a manufacturing facility and then trucked to the site for installation. This is the more typical type for residential construction. Removable forms are what most think of for foundations. However, when casting above grade, foam insulation is typically placed in the forms before pouring begins. This results in a solid wall with high thermal mass.
Log and Timber Home Building – Log and timber home building has been around for hundreds of years. The process of harvesting and drying the logs and timber have improved over the years. Methods to seal areas between logs and at mating areas of roofs and walls have improved. However, log homeowners are like Harley owners, they are looking for a specific feeling from the product and not everyone is looking for that. Log and timber homes continue to be a part of the building systems industry but will never be a mainstream building system.
Modular Home Building – The term “modular home” is really a misnomer. It is a term for a home that is built using modular construction. Modular construction consists of many modular subassemblies built and assembled in an environmentally controlled factory that are assembled into a larger component, or module. That module is then shipped to a building site, combined with other modules, and assembled into a finished product.
Many have heard that since the great recession, there is a labor shortage in the building industry. This means that quality labor is hard to find. The best subcontractors that are out there, because of supply and demand, are raising their prices, thereby increasing the cost of new home building. Modular construction allows a builder to control his costs by having much of the home built in a factory. The plumbing, electrical, mechanical, and many interior/exterior finishes are completed in a factory. This reduces the need for dependence on expensive onsite labor. Most homes built using modular construction are delivered to the site 65-85% complete. Weather, as a factor in construction, is virtually eliminated. A healthy living environment is promoted by keeping rain and moisture out of the home and its walls during construction, unlike with traditional site built homes, reducing the risk of mold and mildew growth.
Building Systems Win(not just in Scrabble)!
Building Systems don’t just win big in Scrabble. Homebuyers that have their home built using a complete building system are the big winners! But when it comes to selecting the right building system, you can perform your own evaluation. We already have. Many years ago, we decided that site built construction just wasn’t the most efficient, healthy, and cost-effective way to build.
We decided that modular construction was the best way to deliver quality custom homes to our customers. We believe in modular construction so much that we won’t work for a customer that will accept anything less than the quality and flexibility that modular construction provides. Modular is the primary building system that we use today to deliver our custom-built homes!
The post Building Systems Win Big in Construction Scrabble appeared first on Impresa Modular.