Modules and Panels and Components, Oh My!
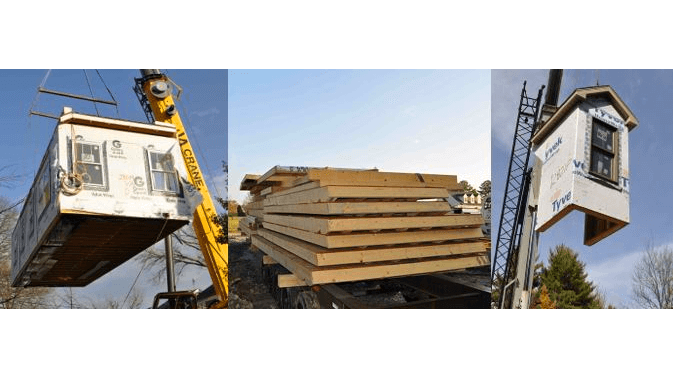
Building technology is changing, but it is only changing incrementally. In the U.S., builders have used what is called light-frame construction as the primary method of building homes since the 1730s. Light-frame construction is a method of construction using many small and closely spaced members that can be assembled by nailing. These members are typically dimensional lumber that is bundled in stacks. These stacks are then dropped off outside at the home site and each 2×4, 2×6, 2×8, or 2×10 is then pulled from the stack and individually cut outside and nailed together with other boards… in the mud, sun, wind, rain, snow, etc. In this method a house is framed and then sheathed (covered) over the course of many days or weeks. Have you driven by a home under construction lately? What did the site look like as you drove by? Was the site organized?
What is a Building System?
For many, they consider a building system something such as HVAC, electrical, or plumbing. structural system. What we are discussing here is the structural system used in assembling and constructing structural elements of a building so that they support and transmit applied loads safely to the ground. Systems-built housing is built using alternative construction methods that utilize various forms of factory-produced items. These items range from simple prefabricated components, such as roof and floor trusses to more complex components such as dormers, porches, or decks. Other factory produced items can include volumetric modular units, open or closed wall panels, and concrete components.
Almost every home today makes use of prefabricated roof trusses. Many homes are also built using prefabricated floor trusses. They are engineered to be stronger, better, and cheaper than their site-built counterparts. Why, because they are built in a factory using high quality materials and under controlled building conditions. They also have to undergo rigid inspections to ensure they meet quality and code requirements.
What is Hybrid Construction?
Hybrid construction uses multiple building systems to deliver high-quality, energy efficient, sustainable buildings at a better value and in less time. New design techniques combine volumetric modules, prefabricated panels, and simple and complex components that are manufactured in a controlled environment to create a higher quality home that is delivered faster than can be had by using just a single building system.
Many builders focus on a single building system. There is an old saying that goes, “If all you have is a hammer, everything looks like a nail’. If a builder will only use a single building system or method of construction, then they are doing themselves and their customers a disservice. Quality, speed, and cost are the three most important to most building a new home. Using hybrid construction gives a builder the tools to deliver the best project to a home buyer. Impresa Modular developed our construction methodology years ago called the Advanced Modular Off-Site Solution® (AMOSS®). It defines our design approach to use volumetric modular construction as the primary construction method and then using panels and components to deliver a project to the homesite at the highest state of factory-built completion. Let’s describe the three primary building systems that make up the AMOSS construction approach.
Volumetric Modular Construction – Practically any home plan can be divided up into modules. With modular construction, each module is structural in nature. It will typically have four sides, a roof, and a floor. Any of these six planes can be built in a temporary fashion until the module reaches the jobsite but the module must be strong structurally for what happens next. These modules are designed so they can then be built in a factory and then placed on a carrier and taken to a jobsite. There, they are usually lifted with a crane and assembled in LEGO-like fashion creating a home or structure. Modules are typically overbuilt from a building code perspective because they have to be built to survive the transport and set with a crane on a home’s foundation.
Panelized Construction – Panels can come in several forms. In their simplest form, a panel that is constructed out of wood is a collection of 2×4’s or 2×6’s assembled into a section of an exterior wall or interior partition panel. This is often referred to as open panel construction. The insulation, wiring, plumbing, and drywall aren’t included in open panels, but some or all of these items may be included in what is called a closed panel. Closed panels typically have methods of interconnecting when installed together. Panels don’t just have to be made from lumber. While wood is the most popular material for residential construction, light-gauge steel (LGS) studs can also be used to create panels.
Component Construction – A component is a part of a building which is manufactured as an independent unit, subsystem or subassembly and that can be joined or connected with other elements to form a more complex item. Roof trusses and floor trusses are what most builders use and blend into the construction of a home built onsite. These items can also be used in offsite construction. Other components can include more complex structures. For example, a number of roof truss-like components can be combined with sheathing to create larger assemblies such as porch sections. A number of porch sections can be shipped to a home site and installed on a home to form a complete, wraparound porch. Other components can include dormers, gables, and rake and eave overhangs, etc.
Hybrid Construction is Resilient Construction
Resilient construction methods create buildings, landscapes and communities designed to better withstand disasters and long-term shifts resulting from climate change. The benefits of resilient residential design strategies include minimizing risks from natural occurrences (such as hurricanes, floods, earthquakes, fires and tornados). With hybrid construction the inherent strength introduced by the connections between modules, panels, and components makes the construction of the home much stronger than a home built using traditional construction.
RELATED: If You Think Off-Site Construction is Risky, Try Traditional Construction
Offsite constructed modular homes built in a factory implement consistent processes and construction techniques. The same resilient design features built into every modular home to withstand transportation and installation also means the home is built to better withstand natural and man-made events at the home site. Construction is regional. With the intentional implementation of additional specific and location specific upgrades, modular homes can be built quickly and efficiently to meet the resiliency requirements needed in any part of the country.
Hybrid Construction Means Your Home is Built Better!
Spend some time evaluating modular construction and learning about its abilities. Study panelized and component construction. Everything you own is built in a factory. That includes most of the items inside your home. Why wouldn’t you demand the same quality and precision for the structure of your home, the shell that protects you and your family. Hybrid construction saves time and money while providing the benefits of healthier living. It’s time to use hybrid construction to build your next home.
The post Modules and Panels and Components, Oh My! appeared first on Impresa Modular.