Modular Brain: Rewiring the Brain for a Better Way to Build
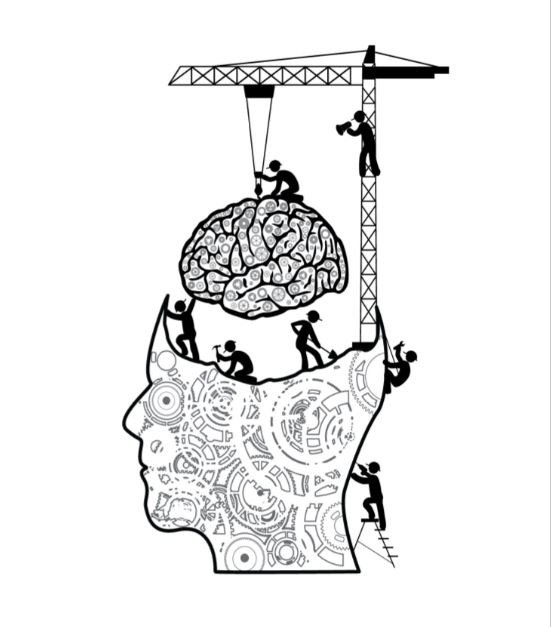
It’s Not a Wrong Way, It’s a Different Way
Construction has remained relatively the same for almost 200 years. There have been some changes overall. Windows and doors aren’t actually built on site any more (yes, they were actually built at the same location as the house was in the 1800’s). Over time the industry discovered it was more efficient to build other things using new technology offsite in factories instead of at the jobsite. Examples are roof trusses and floor trusses. Roof trusses really didn’t start to come into use until the late 1960’s and early 1970’s. Floor trusses soon followed.
For most people, practically everything they buy or own was built in a factory. It includes their phone, their furniture, their clothing, and their car. Consumers, or home buyers in this case, expect the quality and efficiency in their products that only being made in a factory can provide. While the home construction industry has adopted some factory-built components into home building, it has been extremely slow to adopt offsite modular construction as the dominate way to build. You have to ask yourself, “Why?”.
There are several reasons that can be cited. But first is a lack of knowledge and understanding. Because construction has been done a specific way for so long, any new ways aren’t easily adopted. Offsite modular construction completely changes construction processes. From estimating and quoting to scheduling and scoping for subcontractors. It is all different. Most builders are small and don’t have the time to learn a new way. For some that try it is very different. As humans if something is different than we expect then it’s wrong. When it comes to a better way to build custom homes, offsite modular construction isn’t a wrong way, it’s a different way!
Modular Design Is Flexible and Attractive
One of the biggest misunderstandings that homebuyers and builders can have when they research adopting modular construction for building their new home is that its inflexible. Modular home design can be likened to an architectural style. If you are building a mid-century modern home you wouldn’t place a Victorian turret on it. That wouldn’t make sense. When you build a mid-century modern home, you have to build according to is characteristics. With the limits of the style create a discipline for the design. It’s the exact same way when designing with modular construction.
The modular construction process, by its name, means that a home’s plan is created and then divided into modules. These modules are then constructed in a factory setting, delivered on a carrier to a site, and then installed on a foundation. With modular construction, the designer takes into consideration the size of the modules, where load transfers take place, and then creates floor plans and features that can be more readily built in a factory and transported to a site. Designers are also taking into account what can be completed at the factory and what features may have an on onsite completion aspect. While modular construction is a popular method of construction for contemporary homes, most homes are designed using traditional styles with lots of visual interest.
Building in Two Locations… at the Same Time
Offsite modular construction means a home is about 65-85% complete when delivered. Percentage of completion is highly dependent on the home style, the floorplan, and the finishes selected. Onsite there is work that needs to completed no matter what building method you use. For example, the drive way, site excavation, and foundation need to be completed onsite before the house can be delivered and installed (there are actually several foundation systems that are also modular and can be delivered on a truck and installed at your home site).
By have construction taking place in a factory and construction taking place on site means you can drastically reduce the time it takes to build a home. Industry projection say that you can expect to cut 30-50% of the build time out of a home construction project.
Modular Construction Delivers Healthy, Energy-efficient, and Resilient Homes
It’s not just about meeting minimum expectations. It’s about providing a home that is comfortable, safe, and healthy. Indoor air quality starts with the construction of the home. It means keeping lumber dry. It means eliminating dust and construction contaminants from the delivered home. It means using products that are free of Volatile Organic Compounds.
When creating an energy-efficient home, it is important to eliminate or reduce the holes or leaks in the thermal envelope. Modular construction helps you create a tight thermal envelope, where you define the line. Now you can ensure that incoming air is filtered (Healthy). You eliminate drafts (Comfortable). You control moisture and humidity (Safe). All of this is delivered because modular construction enhances energy-efficient construction.
Modular homes built in a factory can implement consistent processes and construction techniques. The same resilient design features built into every modular home to withstand transportation and installation also means the home is built to better withstand natural and man-made events at the home site. Modular homes can be built quickly and efficiently to meet the resiliency requirements needed in any part the country.
Modular Means More
It’s time for the home construction industry to rewire their brains to embrace now how homes will be built, will have to be built going forward. Smart builders and smart homeowners are learning about the key advantages of modular construction. The custom home building industry is one of the last industries to embrace the advantages that every other major industry and product has discovered with modular… factory production. The changing construction labor force and demand for better and consistent quality are now driving the entire custom home building industry to find a better solution. Home buyers and home builders alike are learning the modular is just a better way to build!
The post Modular Brain: Rewiring the Brain for a Better Way to Build appeared first on Impresa Modular.