Are We About to See a New Normal in Home Construction?
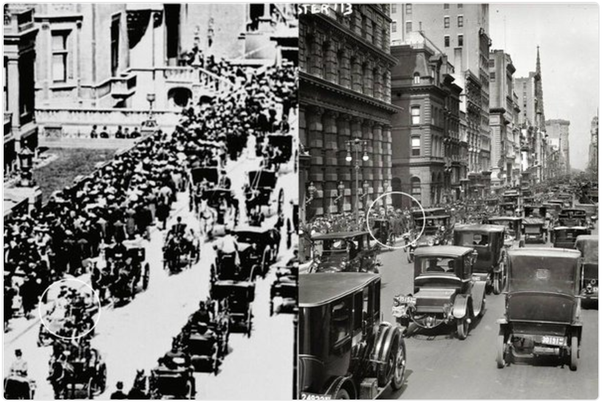
Perhaps the most famous quote attributed to Henry Ford is this: “If I had asked people what they wanted, they would have said faster horses.” While most people agree that Ford never actually said this, it does illustrate a great point. People don’t know exactly what they want until they see it. But once they see it, they will flock to it in droves. And typically when they do, it will happen fast! The main picture in this article illustrates this exact point. The picture on the left was taken on 5th Ave in New York in 1900. You see just one car. However, in just 13 short years there was a complete change. In that same area of 5th Ave in 1913 try and spot the lone horse.
Horses and Houses
So, what do horses and houses have in common? Man (and Woman) has used the horse as a way to move themselves and materials across this earth for thousands of years. While many tried to improve the process by creating different breeds of horse. Even with providing them with better food or better training, using horses as transportation hasn’t improved much over those thousands of years. However, they got the basic job done.
Home construction has pretty much been the same way. In fact, since the early 1800s, there has only been one change in the way homes are built. That occurred just after 1900 with the “invention” of platform framing. And that was driven by the fact that it was harder to get 20’ long 2×4’s and in addition, balloon framing (the old way of framing) created a fire hazard in homes by providing drafting to feed fires that got started inside the home. Other than that, home construction has remained virtually unchanged for almost 200 years!
Something’s Gotta Give!
When it comes to home construction today, we find ourselves at about the same point the transportation industry was at in the early 1900s. Productivity in the construction industry hovers at the lowest rate of any industry in the country at just about a 1% increase in the past 20 years. With all of the technology and knowledge, we have in this country we haven’t been able to significantly improve the way we build homes in almost 200 years.
If you ask a homebuyer what they want in a home they will tell you lower costs, energy-efficiency, and better comfort. They want a faster horse. But that horse still comes with all of the deficiencies it has always had; it was built outside in the rain, subject to construction by unskilled workers working in skilled positions, and being built with the minimum quality possible. The car has been invented!! It’s time to change the way we build homes and deliver housing with offsite modular construction!
Modular is the Offsite Answer
Homebuilders today are struggling to build homes the old way. Utilizing modular construction means the homebuyer and the homebuilder get to take advantage of this better way to build. It can be summed up with the 3 P’s of offsite modular construction:
PRODUCTIVITY – Traditional home building is wildly inefficient. Every home is built in a different location. This means that each home project requires the mobilization of tools, equipment, materials, and labor at a different location for every job. Home construction is a large job and each home has thousands of pieces and parts. It requires a combination of many skills and trades to assemble those pieces and parts into a functional and efficient home. Add to the mix that it takes place outdoors in the elements and you have to wonder how a home is ever actually completed!
RELATED: Are we Approaching the Modular Tipping Point?
Modular construction takes keys parts of the home building process and converts it from a construction process to a manufacturing process. A manufacturing process has twin goals: increase efficiency and reduce costs. This is balanced with the requirement to do both while delivering the highest quality product. Modular construction moves the construction process indoors to a single location where 75-85% of a home is completed.
PROCESS – The majority of American workers today work indoors. It can be in an office or in a factory. They take for granted what that actually means. Let’s list some work characteristics that may seem absurd at first:
- Level floors in the workspace
- Air-conditioned space
- 4 walls and a roof on the building/work area
- Regular work schedule
- Single location
It is very easy to create consistent processes, hire employees, and provide quality products when you have a stable work environment with the above characteristics. Now, throw all of that out the window!
Traditional construction has virtually none of these. Homes are built outdoors, subject to random terrain, bad weather (which leads to missed workdays), and long travels to different job sites for workers and materials. Yet home buyers have the same expectation of cost efficiencies, schedule stability, and quality for their home much like they would if they ordered a new car. However, the environments in which they are created are night and day different!
Modular construction helps eliminate many of the variables in home building by introducing a level of control into the process. Bringing the construction process indoors into a controlled environment is a key element in exponentially improving the construction process.
Modular homes are built indoors. The modular construction process allows a factory to schedule production. Because weather doesn’t impact construction, materials can be purchased and delivered (to a single location) using a just-in-time schedule. Workers that can depend on a full week paycheck, that isn’t dependent on the weather, are more stable employees. When employees have consistent work environments they perform better, delivering a higher quality product.
Quality is better monitored when building indoors. The modular construction process allows for better material usage efficiencies and reduced waste. By employing workers at a single site, creating efficiencies, and reducing waste, homes are able to be built at a better value.
PEOPLE – It’s no secret. Most high school guidance counselors aren’t encouraging today’s youth to pursue a construction career path. This, combined with the massive loss of construction workers after the great recession, has created a crisis situation in the home building industry. The demand for skilled construction labor far outweighs its availability.
However, homes still have to get built. Traditional home builders are at a crossroads. Turn down work because they don’t have the skilled workers to deliver homes or, place unskilled workers in skilled work positions and hope for the best. What do you think happens in this situation?
One of the advantages that modular construction has is that it concentrates the construction of so many homes in a single location. It is a building process, not a one-off project as it is with the traditional construction method. A factory is built on a process. Processes are taught, work is reviewed, and quality is inspected. Just like in any factory process, defective work is identified and corrected.
What modular construction actually does is allow unskilled workers to be utilized efficiently in the construction process. Training is given and supervisors and quality inspectors are able to review work output. Remember, in traditional construction that the only inspections (if any) are performed to ensure building code is met, not to ensure quality. Factories are incented to make sure quality is built in. For example, it may cost ten dollars to correct a quality issue in the factory. However, that same issue may cost five hundred dollars to fix it once that home arrives at the job site. Where do you think the factory would rather correct this issue?
The Future of Home Building is Offsite Modular Construction
The future is in off-site construction. Will the industry change significantly in 13 years like the 5th Ave picture? Probably not. But we have turned the corner. Homebuyers don’t necessarily know they need a new way to build, but the industry does. Commercial construction has embraced modular construction for years. Hotels, office buildings, medical facilities, assisted living homes, etc. All of these projects are being completed with modular construction.
Most custom builders have struggled for years to embrace the rise of modular construction. However, the internet has become a tremendous resource for home buyers building a new home. Today’s home buyers are doing the research. They are learning about the advantages that modular construction provides. They are learning about the difficulties that the construction industry is having with labor and the resulting issues it is causing in new home building. Today’s home buyers want more. The more homebuyers learn about modular construction and its benefits the more they are demanding it. They are ready for the new normal of building homes using modular construction. Homebuyers are ready to trade in the horse for a much better method of transportation!
The post Are We About to See a New Normal in Home Construction? appeared first on Impresa Modular.