Building Beyond Code
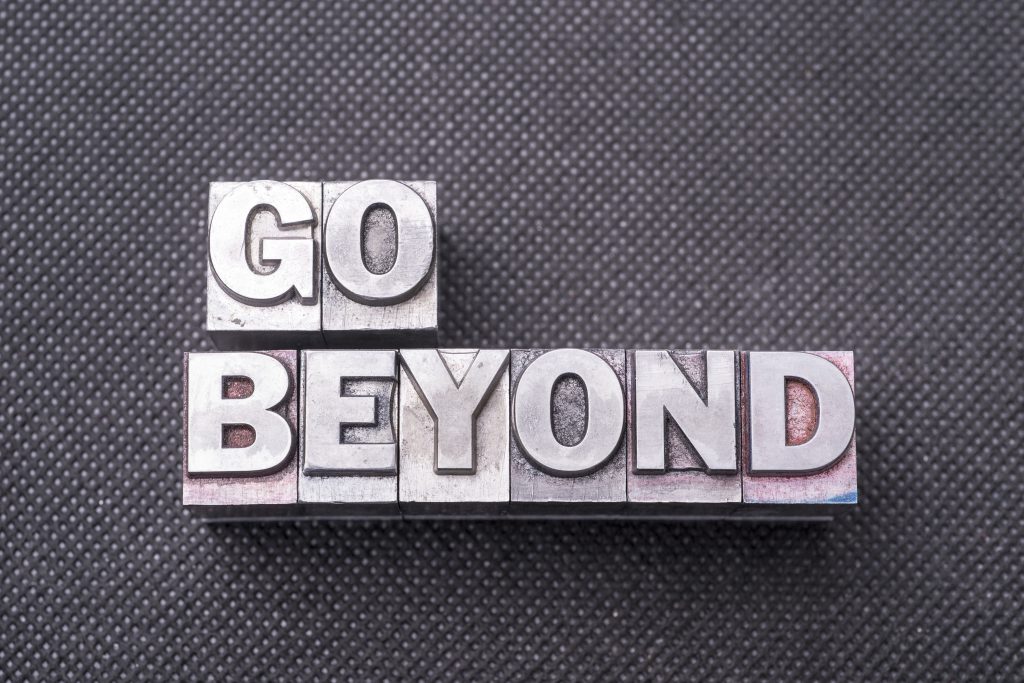
The first principle to understand in modular residential construction is that modular is just that, a type of construction, not a type of home. While the term modular home is the well-worn industry description and I’ll use it in this article, it is a misnomer (i.e. wrong or inaccurate name or designation). Simply put, modular construction is a method of making a home plan and redesigning it to be built in modules off-site in a factory. Those modules are then transported to the home site where they are assembled in LEGO-like fashion on a permanent foundation. Once completed, a modular home is indistinguishable from a home that is built onsite. However, one of the unseen big differences is that the modular home had to be built to take the punishment of being transported on today’s highway system, placed on a home site, and then lifted by two to four cables and placed on a foundation. Let’s talk about what that means for the home buyer.
What is “Code”
The Wikipedia definition for building code is a set of rules that specify the standards for constructed objects such as buildings and nonbuilding structures. Buildings must conform to the code to obtain planning permission, usually from a local council. The main purpose of building codes is to protect public health, safety, and general welfare as they relate to the construction and occupancy of buildings and structures. The building code becomes the law of a particular jurisdiction when formally enacted by the appropriate governmental or private authority.
While that sounds straight forward, it starts to get complicated very quickly. At the national level for residential construction, most states have adopted the International Code Council (ICC) International Residential Code (IRC). The ICC updates the building code every 3 years. For example, there are versions for years 2009, 2012, 2105, 2018, and soon 2021. Now, to complicate things even more, when a specific year’s building code gets adopted at the state level a state may adopt it but leave out certain parts or modify certain parts. Then there are local jurisdictions. In some of the commonwealth states, a local township or entity can create their own unique set of modifications to “the code”.
Who Verifies It’s the “Right” Code?
The next question is, how do you know if you met the right building code for the location where you are actually building? Here is the real shocker for most home buyers building a home. In perhaps half of the United States, the answer is NO ONE if you are building onsite! That’s right, no one! There are no permits or, if there are permits, there are no inspections. And in most of those areas, builders don’t have to be licensed. That means there is no testing and no requirement to have builders participate in continuing education to keep up to date with current health, safety, and construction standards and codes. Codes change on a regular basis and half of the country’s builders and localities aren’t keeping up.
RELATED: The Devil is in the Details
Now, if you are building using modular construction, there is a completely different process. Most states manage and oversee modular construction at the state level. Because construction takes place in a factory the process is in place to ensure public safety and that current standards are met. Each state delegates its review authority and inspection authority to a number of 3rd party engineering and inspection firms. A new modular home plan is reviewed for code compliance. Once approved, during the construction of the modules for that home, inspections are done in the factory and documented to ensure that in fact the home is constructed per the approved plans. This is actually easier to manage because the construction of so many homes are concentrated in one location. So, even in states where there are no permits and no onsite inspections, as a home owner, you can feel good knowing that at least the factory portion of your home was built AND inspected to the current standard.
Building Beyond the Code – Resilience
Ask a builder that builds onsite how he builds his/her homes and they will say that they are built to meet current building code. What they are really saying is that they are providing you with a home that is built to the lowest standard currently allowed by law.
When you choose to build with modular construction, you have a home that is built using a consistent process, that is built indoors, and that is inspected to meet the current building code in place for the state that it will place. But in addition, your home’s modules will be overbuilt. It has to be transported down the road on a carrier at over 65 mph and then lifted by a crane with wire cables and placed on a foundation. All of this with no or minimal signs of the effort. All of this can be done only when the structure of your home is designed and built to typically exceed your localities minimum building code.
This toughness translates to resilience. Resilience in construction is the practice of using construction materials and techniques that increase a structure’s ability to withstand adverse weather and changing climate conditions. It typically includes constructing a home with a tighter building envelope and using stronger materials.
Thinking Past the Code
When building the modules for a home in a factory, it is the perfect time to add in the additional structural features for modular’s enhanced construction. These enhancements can include:
- Using lag bolts and/or screws at corners and where interior walls meet exterior walls.
- Screwing, instead of nailing, wall foot plates to floors.
- Using additional strapping to connect floors to walls and walls to ceilings.
- Using longer sheets of OSB called TallWalltm to connect floors to walls and walls to ceilings with one contiguous connection.
- Use of industrial adhesives over standard adhesives to connect drywall to studded walls and to attach drywall to ceiling assemblies.
These features just strengthen the basic structure of each individual module. Once on site, each of these modules is then connected to the foundation and then each other. The inherent strength created by attaching individual units just makes the overall structure that much stronger creating a safe and protective environment for the occupants of the home. This enhanced strength has been noted by FEMA in its report following Hurricane Andrew.
When it comes to energy efficiency just think about the last time you drove by a construction site where a home was being built… one stick at a time. Was it raining? Was the wind blowing? Was it a flurry of skilled workers building from a detailed plan to ensure each assembly was installed and connected properly? Were component connections sealed with gaskets, foam, or caulk to ensure that there was a tight thermal envelope to improve energy efficiency and enhance indoor air quality and comfort? Now imagine if that was a factory built modular home.
Modular Means More
The simple fact of turning construction into a manufacturing process and building indoors is at the heart of the benefits provided by using modular construction. A modular home is built indoors in environmentally controlled conditions. You can be assured that the same high quality is achieved year round when constructing your home. In fact, even the same cost efficiencies of modular construction apply year round. Modular means that you are getting a home that delivers on comfort, safety, design, and strength. Modular just means more!
The post Building Beyond Code appeared first on Impresa Modular.