How Can Modular Construction Mitigate Home Building Delays?
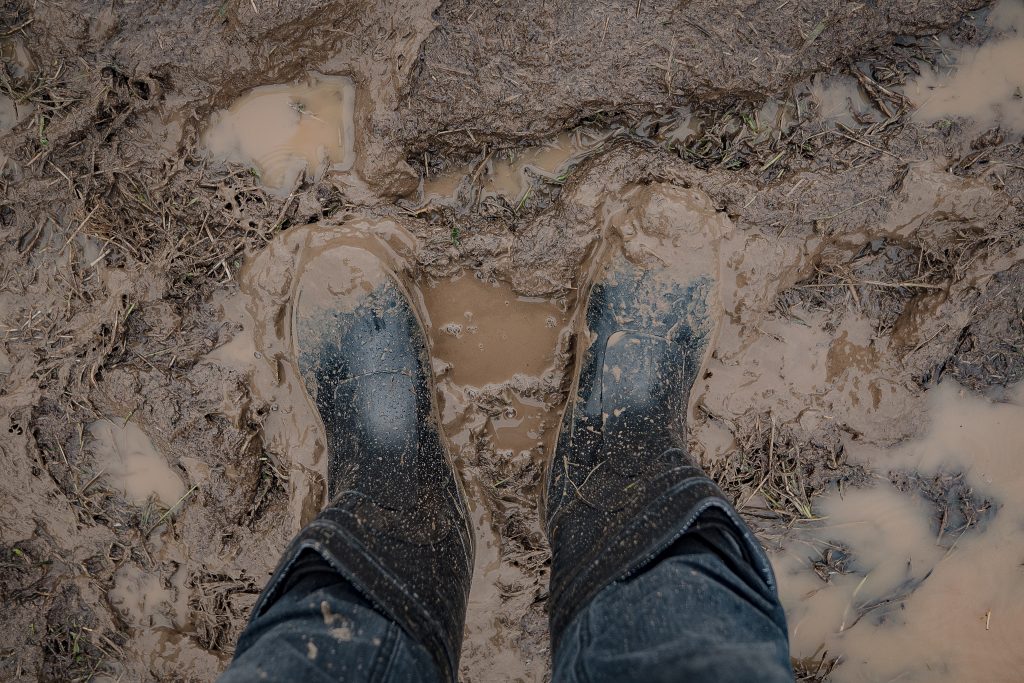
Building a custom home is not for the faint of heart. It is a process that will take time, effort, and patience. A custom home is unique. It has never been built before. Add to that the process of constructing it on an individual building site with its own unique characteristics. And then you are doing all of this outdoors in the weather. To build a custom home successfully is a process that takes patience, knowledge and excellent project management skills.
Avoiding construction delays starts with recognizing their most common causes and working to mitigate those factors before they can impact the home building project. Planning is crucial, but it also depends on close oversight and an understanding of the process to determine when things are falling behind and then making the right decisions and taking the right steps to keep a custom home building project on track. Here are the four most common causes of construction delays and how using modular construction can help to mitigate them.
Bad Weather
Bad weather such as rain, snow, and high winds can really delay a home building project. In most areas of the country, rain is the main cause of construction delays. What most builders fail to communicate to their customers is that weather delays aren’t a one-for-one trade off. What that means is that one day of rain doesn’t just mean one day of delay. For excavation, one day of rain can mean at least three days of delay while the soil dries so it can be workable again by excavation equipment. If it rains again in those three days, then the clock starts over again.
Another aspect is construction subcontractor management. A subcontractor has to keep his employees and equipment working. If a project in one area gets delayed by weather but that same subcontractor has a project within his work area that isn’t impacted by weather, they will start that project. Once a project is started most subcontractors like to stay on the site until it is completed. For example, a home’s foundation excavation and driveway construction may only be a two day effort. However, it rains on the day the excavation subcontractor was supposed to start. If they can move to another site and keep working, they will. But the other site has seven days worth of effort to complete. This means one day of rain just resulted in seven days of delay because they worked to finish the other project before moving back to the original site.
Modular construction can’t mitigate site issues but it can help with other construction delays. It never rains in a factory. Construction of a custom modular home continues no matter the weather. Modular means that construction in the factory is happening while work is happening at the home site saving months in construction scheduling.
However, even with modular construction, site issues can cause delays during the critical home delivery and installation phase. It takes the coordination of up to four things to install a typical modular home: the actual delivery of the home modules, the availability of the installation/set crew, getting a crane on the site and possibly having equipment be available to move the modules around on the site. All of these items have to be available on the single day of the home installation. A rain delay can mean that all of these participants must be rescheduled.
Overbooked Crews
Many home builders and subcontractors take on too many projects. They overbook their crews knowing that weather delays or other schedule delays can cause downtime and they have to keep their crews and equipment working. However, this can lead to them falling behind on one or more jobs as their exhausted employees drive around from job to job each day trying to get everything done.
Good project management and relationships with subcontractors can help mitigate this issue for home buyers. General contractors that have excellent reputations for on time delivery of projects get that reputation because they have a stable of good suppliers and good subcontractors and have the ability to get them to give their job sites a priority when scheduling. Using modular construction means that most of the work is done in a factory. A small project for a subcontractor can mean a quick completion (and a fast payment). In many cases, subcontractors prioritize getting modular projects done so they can get to their next larger project.
Unreliable Subcontractors
For onsite construction, subcontractors that waste time on the job site is a plague in the construction business. On the one hand, they may lack the tools, training, experience, or methodology that’s needed to get the job done efficiently, but on the other hand, they may spend too much time chatting or on coffee breaks and lose focus on the importance of timeliness on the job.
Modular construction means that up to 75% of a home building project is completed in a factory. This means that many of the inefficiencies of building outdoors are eliminated. There isn’t the wasted time of waiting for one subcontractor to complete their work before the next subcontractor can start. There isn’t the wasted time of multiple crews spending hours driving to a unique home site. Modular construction concentrates the building of many homes in one location. All of the tools are already there. All of the materials are already there. The typical excuses for why work didn’t happen on a site built home don’t play out with modular construction.
Unexpected Changes/Change Orders
Unexpected changes are always going to be a part of the construction business. It could be that during the foundation excavation that rock was discovered. Or, it could be that an unexpected permit delay occurs. This happens and sometimes in just can’t be controlled. However, change orders can be controlled in most cases. During construction for a site built home, the home reveals itself over time. As a customer walks through a home under construction it seems a room is too small. A change order is processed to move a wall. Change orders just don’t add cost to a project. Most change orders also add time to a project. Change orders requiring special materials or items can add significantly to a project if that item is in the critical path for project completion.
With modular construction, the early design and option selection process can be longer. This is because everything has to be decided up front. There isn’t going to be six or nine months of time to move walls or select colors. It all has to be decided in the beginning so materials can be purchased and the custom home scheduled for a project in the factory. This because once a home starts construction in the factory, the factory portion will be completed in days, not months! Because of this, most change orders are reduced or eliminated with modular construction. This typically has a very positive impact and reduces delays in the construction process.
Modular Means Better Scheduling Control
Because of the efficiency of the building process, you can get the superior quality of modular construction in less time. While the portion of construction that happens outside of the factory can be subject to typical project delays, modular means better overall project scheduling for delivery of your new custom home. Modular takes home construction to the next level. Modular means more!
The post How Can Modular Construction Mitigate Home Building Delays? appeared first on Impresa Modular.