Modular Will Win the Construction Method Street Brawl (and these will be the lessons learned)
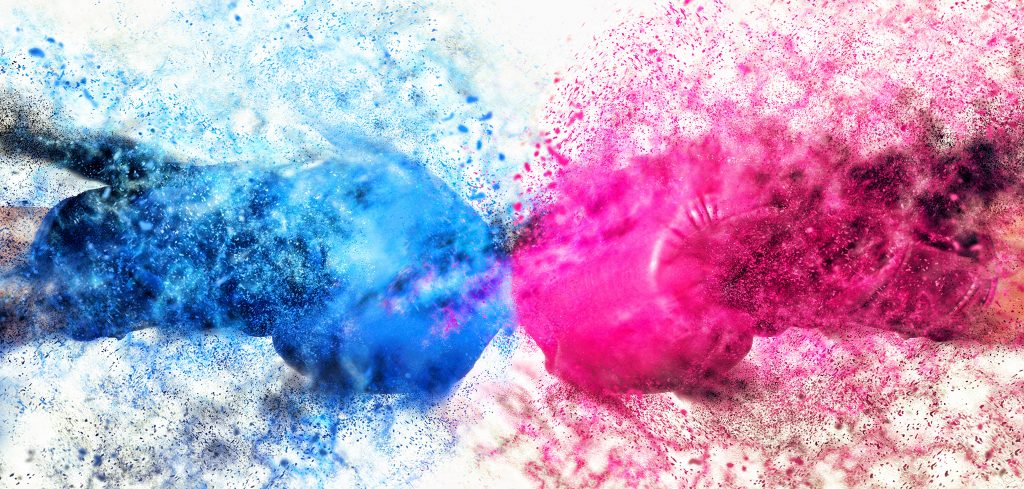
Today, the construction industry is in a street brawl with itself. Never before has it faced the concurrent accumulation of this many issues at one time. To start with, America is behind on building homes. Given various reports, as a country, we need to build over 300,000 more homes than we are currently building each year to keep up with demand. In addition, we don’t have the labor, skilled labor, needed to build the homes we need. As an industry, productivity continues to fall in construction, and we can’t make it up with people. Building systems offer the only way forward in the current environment. In the end, modular construction will be the new traditional way that American builds its homes.
First, We Had it… But We Lost It
Throughout the history of home building in the U.S. there are many examples of building homes in factories. But, because the onsite method of building has had such a long time to grow and establish itself, it has become the ingrained way to build. The entire support industry; tooling, materials, and now software supports building onsite. However, we can’t continue to do it that way. As an industry, we know building onsite isn’t sustainable going forward. Today, large production home builders to small custom home builders are researching off-site construction.
There are several building systems that exist today. These include concrete panels, open panel wood construction, closed panel construction, and modular construction. Each of these building methods offers some way to take advantage of concentrating construction of components or modules for many homes in one location off-site and then transporting the factory built components to the home site for final installation/assembly.
RELATED: MODULAR CONSTRUCTION: BRINGING THE FORCE MULTIPLIER EFFECT TO HOME BUILDING
Modular bungalows were available in the early 19th century. Henry Manning, a London carpenter, produced the Portable Cottage in 1837 for export to Australia. The California Gold Rush of 1848 saw imports of prefabricated houses from Britain, Sweden and China arrive to house the 49ers. When there was a need for homes but labor wasn’t available or locations were remote, modular construction has stepped in. Off-site modular construction has been available and used for almost 200 years. But, when labor becomes plentiful and resources are cheap, the industry does what is easy for it. It builds homes onsite.
Second, Panelized Construction is a Step in the Evolutionary Path of Home Building
One of the off-site building systems is panelized construction. It has found favor with many production builders that are trying to dip their toes into off-site construction. This is probably because it is the off-site building method that changes their home building processes the least. Adopting a new way to build is hard. Many changes have to take place to adopt a better way to build. Just like with changes to improve your personal life, the pain of staying (old methods) has to become greater than the pain of moving to a better method or the change doesn’t occur.
The limitation of panels is that they only speed up one small part of the onsite construction process, the framing part. After that, everything else still has to be done onsite. All the trades and subcontractors are still being scheduled and still working in the weather. Materials are still being delivered to each and every remote home site. While building with panels is better, it is only incrementally better.
For the construction industry, panelized construction’s evolutionary path is to keep the panels in the factory and further assemble them into larger modules. In the factory, these panels can be placed on floor systems and have roofs/ceilings installed. Once that is done, all the trades can work under one roof to complete these modules to a much higher level of finish. Trained workers can install insulation, drywall, flooring, trim, cabinets, tile, etc. All this is done underroof and in a controlled factory environment. Instead of delivering 50 – 80 panels to a site for assembly (and that still requires full finishing) as few as 2 or 4 modules can be delivered that are substantially complete.
Third, the Construction Industry always does the right thing…but only after exhausting every other option
The construction industry is quickly coming to a crisis. It is one of the few modern industries in which productivity has remained flat (or even decreased slightly) over the last 50 years. Even with the invention of nail guns versus hammers and the proliferation of just about every battery operated tool imaginable, the industry just can’t seem to build better homes faster.
The great recession changed the labor market and there just aren’t enough workers entering the construction trade. Trade schools aren’t keeping up. To entice higher skilled workers, contractors have to pay more. When it costs more to build a home, those costs get passed on to home buyers. The cost of building a new home keeps going up making homes less affordable. The answer has been here for almost 200 years. The Advanced Modular Off-Site Solution (AMOSS) is the way forward for home building. It just makes sense!
The post Modular Will Win the Construction Method Street Brawl (and these will be the lessons learned) appeared first on Impresa Modular.