Confused by Home Building Lingo? Let’s Decipher It.
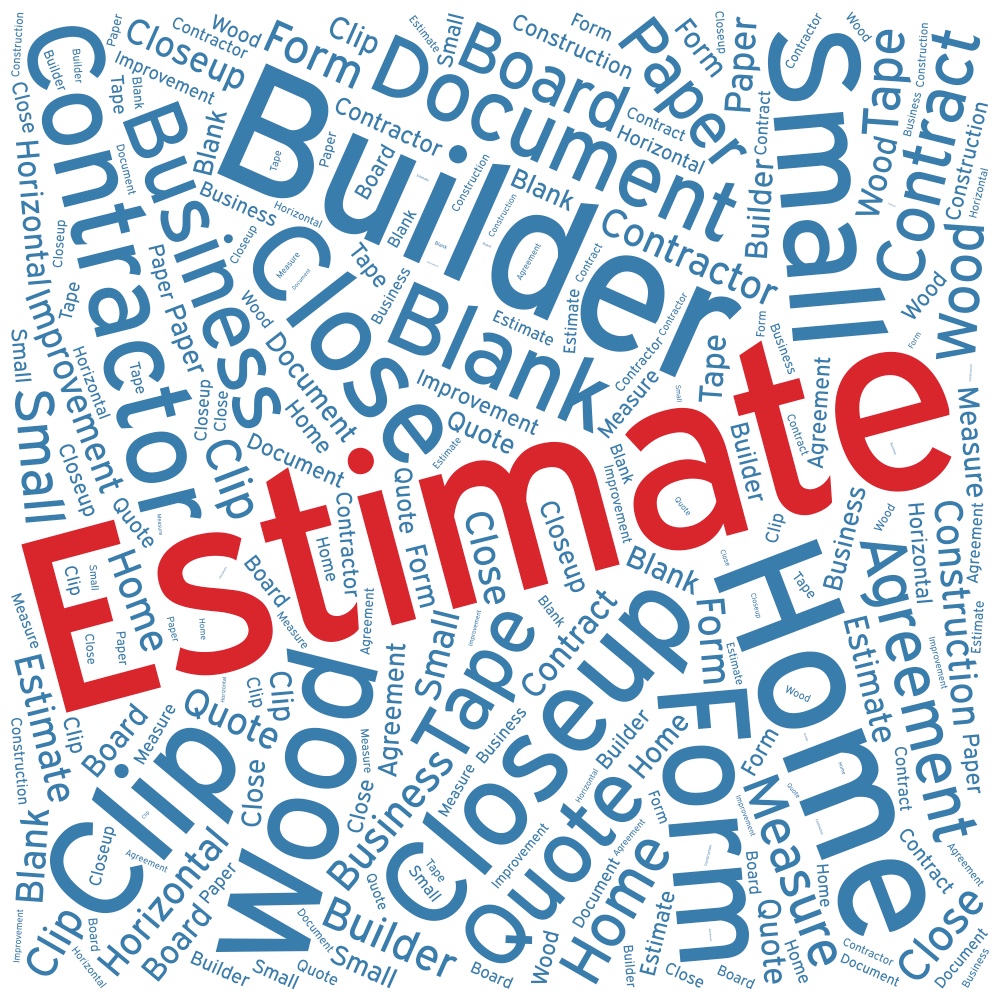
Most homes purchased are used/existing homes. What you see is what you get. You don’t get to have any input into the design of the home, the construction of the home, or the way the home is built. When building a new custom home that all changes. There are hundreds of decisions to make and hundreds, if not thousands, of new terms to learn that are unique to home construction. If you are like most people, you are usually too embarrassed to ask what a term means. It is easier to take the “smile and nod” approach and avoid asking about a term you don’t understand. It is important to understand key terms used in home construction when building a new home. Here is an explanation of a few of the more common terms in home building.
Building Code/Construction Types
IRC – International Residential Code – There used to be many codes and many versions of that building code that were adopted by each state. Over the years most states have adopted the IRC. The IRC is updated every three years. For example, a state many adopt the 2012 version of the IRC. Until it votes to adopt a new update, they may skip several updates. They could choose to wait until 2021 to adopt the next version.
Stick Built – Stick built is a term that is used synonymously with onsite construction. This is the way homes have been traditionally built in the U.S. for two hundred years. Every part and piece needed to build a home is delivered to a home site. The construction workers travel to that home site everyday bringing their tools with them. Over a period of time, they cut each piece outside building a new home over a period of months.
Offsite Construction – Traditionally built homes are built onsite, outdoors. Off-site construction attempts to take advantage of building indoors. Sub-assemblies, components, and even large modules are constructed indoors in a factory setting (much the same way a car is built). Because the workers, tools, and materials are all in one place, each day – every day, efficiency and quality are improved with off-site construction. The pieces that are built off-site are then transported to the home site and used to assemble the completed home.
Modular vs Manufactured Home – This is a point of confusion for many. A manufactured home is built to a different building code, called the HUD code. It is a Federal Building code that allows homes to be built more economically for affordable housing. These are commonly called mobile homes or double-wides. Modular is not a type of home, but rather a method of construction. A home plan is divided into modules and built off-site. It is then assembled at the home site. It must be built to the same local building code requirement as a home that is built onsite.
Common Roof Terms
Gable Roof – A gable roof is one of the most common roof styles. It is usually identified by a long peak or ridge with two sloping sides. It has a “triangle” on either end. It can be combined with other roof styles and is commonly used for porch roofs.
Hip Roof – A hip roof doesn’t have triangles. It has a sloped roof on all four sides. Hip roofs are more common in the south. They are also more common in high wind areas. Hip roofs are more complex to build and therefore typically add more to the cost to construct a home.
Eave – The eaves are the edges of the roof that overhang the face of the side walls of home and usually project beyond the sides. They are functional in that they shed water further away from the foundation and can be made wider to help shade windows from sun.
Rake – The rake is not exactly on the roof. It is a term that describes the sloped sides on the end of a gable roof (the top sides of the triangle). The rake can be flat with no overhang, or it can overhang the gable end like an eave. The overhanging rake then is closed in with soffit and fascia or left open.
Fascia – Fascia is the horizontal board which caps the end of rafters on the eaves outside a building. It may be used to hold the rain gutter. It is also the name used for the board on the finished the rake on the side of a gable roof.
Soffit – Soffit is the finished surface below the fascia and rafters. When standing under the eave or the rake it is what you see when you look directly up. It may be solid or may be perforated to promote air flow and ventilation into the roof.
Parapet – Parapet is a feature that is commonly used in commercial construction. Most residential construction offers some type of sloped roof. However, with modern architecture, flat roofs are a common feature of that style. A parapet is a small wall that extends above the edge of the roof. It actually has a function in that it dramatically reduces the ability of high winds to lift and peel off a flat roof structure.
Dormer – A dormer is added on top of a roofs structure. Most of the time it contains a window on the flat end of the dormer. Dormers come in many styles that can reflect the roof style, such as gable or hipped. They are typically used for two functions; to provide a way to get light under the roofed area or to create additional space under the roof in a loft area (think Cape Cod or chalet style home).
Construction Terms
O.C. – This is short for “On Center”. This term is typically used to describe the spacing between studs, floor joists, or roof trusses/rafters. Common examples are walls that are spaced 16 inches O.C. or 24 inches O.C. The traditional thinking was that 16 inches O.C. was better quality. However, with modern construction techniques and the new requirements for higher energy efficiency, 24 inches O.C. can provide a greener, more energy efficient home.
Dimensional Lumber – Solid lumber is called dimensional lumber. Some terms seen and heard are 2 x 4, 2 x 6, and 2 x 10. For example, a 2 x 4 means a piece of lumber that is 2 inches deep by 4 inches wide. However, that is not its true size. The actual finished size is 1.5 inches by 3.5 inches. This is because the board is dried and planed (smoothed) which reduces its size from its original cut.
OSB – Oriented Strand Board – OSB is made from shredding logs into chips. Giant machines take the chips and orient them in a specific pattern and thickness. Glues/adhesives are then combined with the chips to create large, flat sheets. These sheets are strong and make complete use of logs. OSB is used to sheath roofs, walls, and floors.
RELATED: WHAT’S THE DIFFERENCE BETWEEN A MODULAR AND MANUFACTURED HOME?
Plywood – Plywood predates OSB. It is still used today but is more expensive than OSB. It is made by “peeling” logs. The layers that are peeled from the log are glued together in a sandwich that can be many layers, or plys, thick.
Truss – Trusses are built for two main reasons, they take less lumber to build (saving costs) and they are stronger than dimensional lumber. The two mainlocations that trusses are used in a home are in the floor and in the roof. Trusses are engineered. Calculations are done to determine how to get the most strength with the least amount of wood using a specific configuration. For example, one specific design uses 2 x 3’s and OSB (Oriented Strand Board) to reduce wood usage and create a truss that has more strength than a 2 x 10. They can be placed 19.2 inches O.C. versus 16 inches O.C. meaning less of them are needed with no sacrifice in floor capacity.
Sill Plate – A sill plate is a layer of treated lumber placed on top of a foundation before floor construction begins. Untreated wood cannot be in contact with concrete or wet surfaces. A home is constructed with untreated wood. A sill plate serves several purposes. One, since most typical foundations are created with concrete, the pressure treated sill separates the concrete from the untreated wood. Another purpose is to act as a barrier from termites because they won’t eat through treated lumber. Another purpose of a sill plate is to act as an intermediary attachment to connect the homes structure to the foundation.
Lally Column – Often mistakenly called a “lolly column”, a lally column is a steel pipe column typically used in basements and crawlspaces to support a home’s structure without building a wall. It is a cost effective way to provide structural support to a home where needed.
Key Contract Term
Allowance – This is a term that is commonly used in contracts for construction. In its simplest form it is a dollar amount in a contract that is allowed for a specific item. For the contractor, he has included up to this amount for the allowance item in his contract price. If the cost of the item goes higher, then the customer has to pay only the amount that the actual cost of the item goes over the allowance. However, if the item costs less than the allowance, then the customer will actually receive a refund for the amount saved. Allowances are tricky, some contractors can use them to artificially make a customer think they are getting more than they are. For example, an allowance for a granite counter top of $1,500. The granite will actually cost $5,500 but the contractor made his initial price artificially lower. Allowances should only be used when specific prices aren’t known at the time. However, a reasonable estimate needs to be used to create an allowance.
These are Just a Few of the Common Terms
There are many more terms that customers building for the first time should be familiar with. Take some time and do some research. Get familiar with construction lingo. Don’t be afraid to ask if you don’t understand something. After you sign a contract and build a home it is too late.
The post Confused by Home Building Lingo? Let’s Decipher It. appeared first on Impresa Modular.