Marriott Chooses Modular for its Luxury Hotels
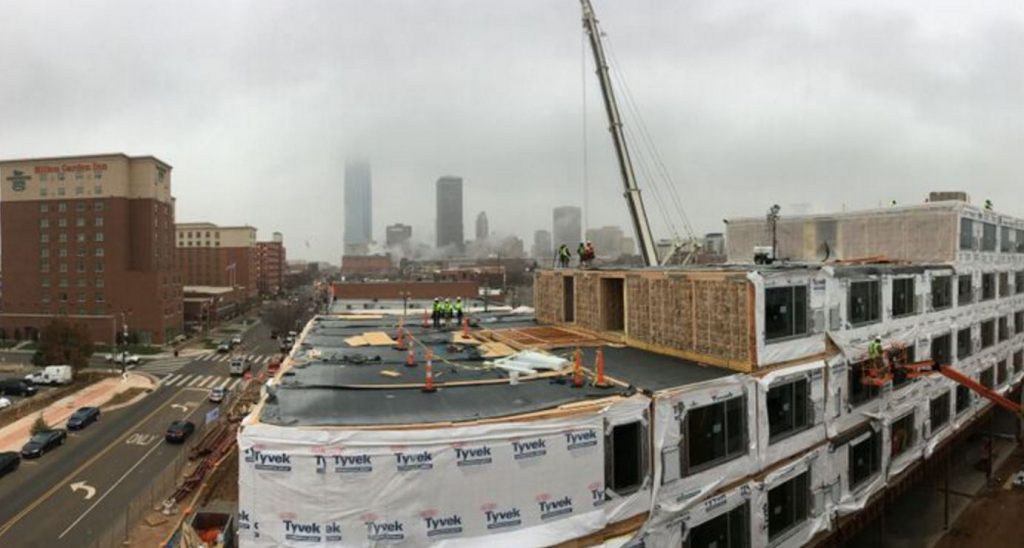
Marriott, one of the best known hospitality brands in America, has taken the plunge. Marriott has found modular and they love it. In fact, they love it so much that they have decided to go full speed ahead and introduce an initiative that will build 50 new modular hotels in the coming year.
The Dilemma Shared by Marriott and Custom Home Builders
Marriott is facing the same issue as every custom home builder in America, a shortage of skilled construction workers. Just like a custom home builder, Marriott requires quality construction for its luxury brand hotels. Not only do they need quality, they need it built quickly and on a budget. Those three items have been proving to be more elusive to the construction arm of Marriott over the last several years.
Since the great recession, much of the skilled construction labor force has retired or found other positions. Whether it’s to build a custom home or a luxury hotel, you need experience and consistency in your workforce. It is even more important for the skilled craftsmen it takes to deliver on expectations that exist in these niches of the construction industry.
Marriott Jumps On Board
Modular construction has evolved in its sophistication over the last 20 years to support custom home building with design flexibility, high end finishes, and consistent high quality. While many builders are just finding out how to adopt it, it has been used by many of the best custom builders for years. It is hard to match the speed and durability of a home built with modular construction.
“Construction is the next frontier for innovation, and modular is leading the way.”Eric Jacobs, Marriott International’s Chief Development Officer of Select Brands, North America – CONNECT Conference
Marriott, faced with the longer construction time frames, quality concerns, and rising prices had to evaluate it options. The traditional way of building just wasn’t working in the current environment. Karim Khalifa, Marriott International’s Senior Vice President of Global Design Strategies said, “We believe the modular process will be a game changer for our valued development partners, especially during a time when labor shortages can be a challenge to timely openings.”
FF&E: Maximizing the Advantages of Factory Construction
While modular construction for custom homes hasn’t moved to this level of completion, the repetitive nature of a hotel room has allowed Marriott to capture another advantage of building in a factory. Think about all of the beds, desks, tables, couches, etc. in a hotel room. In the hotel business, this is called FF&E: Furniture, Fixtures, and Equipment. Now imagine a 150 – 200 room hotel that has to be filled with FF&E after the hotel construction is completed. How long does it take and what damage happens to hallways, elevators, and the rooms by workers as the furniture is moved into place?
Marriott orders their modular hotels with FF&E as part of the contract with the factory. This means the factory not only builds a module, which typically contains a completed room on either end with a part of the central hallway, it also puts the furniture in every room. All the truckloads of furniture are delivered to the factory, workers place every piece in the room, strap all of this to the floor temporarily for transport, and then seal the door.
Onsite, the only actual construction (and associated mess with connecting and finished the new stacked modules) that takes place is in the unfinished hallway. Upon completion, a final team of construction workers put on white booties and enter each of the sealed rooms to remove the strapping. The factory fully constructed the room including the bed, desk and toilet, including the sheets and pillows in the closet and along with a high-definition television ready for viewing. Once completed, each room is immediately ready to be used by a hotel guest.
Modular Construction Delivers on the Promise – for Hotels and Custom Homes
Marriott spent years evaluating modular construction. In the European hotel building business, modular construction has a higher percentage of the market because of the higher labor costs. Now that labor cost and availability has become an issue in the U.S., hotels are being driven to adopt modular construction as the preferred method of building their hotel brands.
With hotels, the construction is typically very repetitive. When you think about a hotel, it is very easy to “modularize”. Each module breaks down into two rooms connected by a section of central hallway. Depending on the hotel brand, the rooms can vary in size, amenities, and overall feel. While the rooms themselves are very standard, the overall hotel design isn’t limited to squares and rectangles. Hotel companies are using the advantage of building in a factory to increase quality, reduce costs, and reduce construction time-frames. Sounds very similar to what is desired when building a custom home.
RELATED: WHY BUYING A NEW HOME IS BETTER THAN FIXING UP AN OLDER HOME
But customers for a custom home require even more… they want broad design flexibility. And modular construction delivers! While factory capability varies across the U.S., the technology and industry have the ability to produce very custom homes that can be built in modules, transported to a home site, and assembled into unique, custom homes.
Guests of the new Marriott hotels mention that the new rooms just feel good. Maybe this is because of the heavier construction… they are just quieter. It could be because they are built stronger and the rooms just feel solid and safe. That same feeling translates into custom homes built using modular construction. They just feel safer, stronger, and quieter.
Modular Construction for Your Custom Home?
Marriott took the plunge. They decided, after years of research, that factory built, modular construction gave them a tremendous advantage when building multi-million dollar hotels. They found that they could build a luxury brand hotel faster, more cost effectively, and with a quality that discerning guests expected and could actually sense.
While most new custom homes don’t cost millions of dollars, the requirements are much the same. Quality, value, and timeframe are important factors in the decision for choosing how to build a new home. Add to that the design flexibility inherent in today’s modular construction and this method is now being chosen by more people who have done the research when it comes to building their custom home.
The post Marriott Chooses Modular for its Luxury Hotels appeared first on Impresa Modular.